Exploring the Wen Lathe Drill Chuck: A Complete Guide
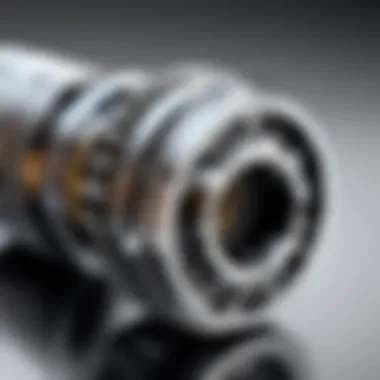
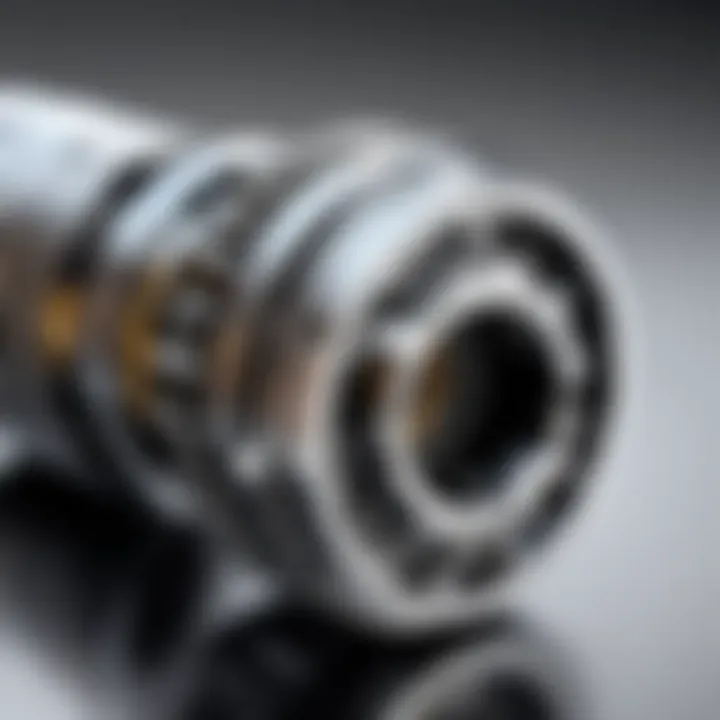
Intro
In the realm of precision machining, the Wen Lathe Drill Chuck stands out as an indispensable tool. Understanding its capabilities and applications can empower both novices and seasoned machinists. This guide aims to navigate through the essential aspects of the Wen Lathe Drill Chuck, shedding light on its construction, benefits, user base, and operational nuances. Readers will glean insights into installation techniques, maintenance tips, and performance optimization, making it a valuable resource for informed decision-making.
Overview of the Product
Purpose and Benefits
The Wen Lathe Drill Chuck is designed to securely hold drill bits in place while the lathe operates. This device enhances the efficiency of machining tasks, allowing for precise drilling and cutting with varied materials. The primary benefits include improved accuracy, versatility in operations, and ease of use—essential factors for anyone working in a machine shop or engaged in DIY projects.
Target Audience
This guide addresses tech enthusiasts, hobbyists, and professionals in the field of machining. Whether one is a beginner eager to learn or an expert looking for advanced techniques, the information provided caters to all knowledge levels, ensuring comprehensive understanding of the drill chuck's features and functionalities.
Key Features
The Wen Lathe Drill Chuck boasts several features that contribute to its popularity:
- Robust Construction: Built to withstand the rigors of industrial use.
- Compatibility: Fits various lathe models, enhancing its utility.
- Easy Installation: Designed for quick setup, minimizing downtime.
- Versatile Applications: Suitable for woodturning, metalworking, and more.
Technical Specifications
Detailed Product Specs
When considering the Wen Lathe Drill Chuck, understanding its specifications is fundamental. Key details include chuck size, thread type, and maximum RPM ratings that delineate its usability across different tasks.
Performance Benchmarks
Performance benchmarks reveal how the Wen Lathe Drill Chuck fares in real-world applications. Users can expect consistency in holding power and precision, resulting in clean cuts and reliable operation.
Installation and Setup Guide
Requirements for Installation
Before installing the Wen Lathe Drill Chuck, ascertain the following requirements:
- Correct size drill chuck for your lathe.
- Basic tools such as wrenches and screwdrivers.
- Safety equipment like gloves and goggles.
Step-by-Step Process
- Prepare the Lathe: Ensure it is switched off and unplugged.
- Remove Existing Chuck: Use the wrench to detach the previous chuck if applicable.
- Attach Drill Chuck: Position the Wen Lathe Drill Chuck and secure it by tightening the screws.
- Check Alignment: Ensure the chuck is aligned properly before usage.
- Test Operation: Run the lathe briefly to confirm everything is functioning correctly.
Tips for Optimizing Setup
- Always lubricate the chuck before installation for smoother operation.
- Regularly check for wear and tear to maintain optimal functionality.
Questions and Answerss and Troubleshooting
Common Issues and Solutions
- Chuck Slippage: Ensure the chuck is tightened adequately.
- Vibration During Operation: Check for proper alignment and balance of the workpiece.
For more detailed discussions, visit Reddit where machinists share their experiences with the Wen Lathe Drill Chuck.
Expert Tips
- Regular cleaning of the chuck will prevent build-up and ensure longer life.
- Keep an eye on drill bit compatibility for best results.
Preamble to Wen Lathe Drill Chucks
Understanding the Wen Lathe Drill Chuck is vital for anyone involved in machining, whether for professional projects or hobbyist activities. This component is essential in ensuring precision and efficiency in various lathe operations. Drill chucks serve as the interface between the lathe and the drill bit, making their design and functionality crucial for achieving desired results. The importance of a reliable drill chuck cannot be overstated, as it directly impacts the machining quality and workpiece accuracy.
Definition and Purpose
A Wen Lathe Drill Chuck is a specialized clamping tool designed to hold and rotate drill bits in a lathe machine. Its primary purpose is to securely grip the drill bit, allowing for the precise drilling of holes into various materials. Depending on the task, the chuck is capable of accommodating different sizes and types of drill bits, enabling versatility. The effectiveness of the lathe largely hinges on the performance of the drill chuck, as a poorly functioning chuck can result in missed measurements and flawed creations.
Historical Background
The evolution of drill chucks traces back to the early days of rotary drilling technology. Originally, devices were rudimentary and often unreliable. The need for improved efficiency and precision spurred innovations in drill chuck designs, leading to modern advancements we see today. Wen's contributions to this field have made their drill chucks popular among both professionals and hobbyists. With growing technology, these drill chucks are now available in various types, catering to specific machining needs. Historical advancements highlight the significance of precision and reliability in tooling, underscoring the Wen Lathe Drill Chuck's role as a trusted tool in machining operations.
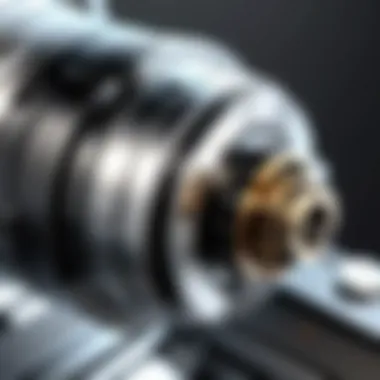
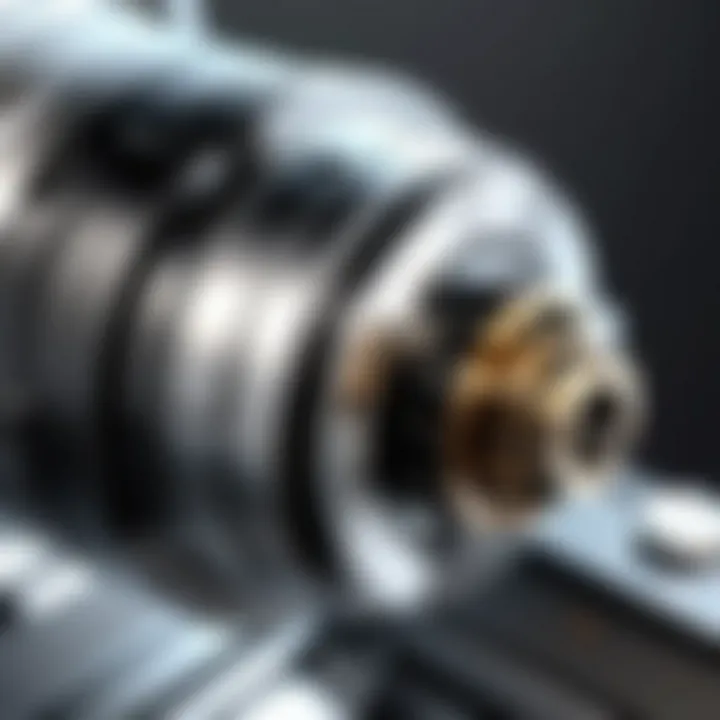
Components of the Wen Lathe Drill Chuck
The components of the Wen Lathe Drill Chuck play a critical role in its functionality and efficiency. Each part of the chuck contributes to its operation, allowing it to securely hold various drill bits and attachments. Understanding these components helps users appreciate the engineering and design that goes into this vital tool. The main components include the body construction, jaw mechanisms, and the chuck key and drive mechanisms.
Body Construction
The body construction of the Wen Lathe Drill Chuck is fundamental to its overall durability and performance. Typically made from high-quality steel or alloy, the body ensures strength and resistance to wear over time. A robust construction enhances the chuck's ability to withstand high torque and keeps it operational under demanding conditions.
An essential aspect of the body construction is the design, which often allows for better centering of the drill bit. This precision ensures that the workpiece receives an accurate cut, which is crucial during machining operations. Additionally, the surface finish on the body minimizes friction and enhances the chuck's performance. A well-constructed body contributes directly to the longevity and reliability of the drill chuck.
Jaw Mechanisms
Types of Jaws
Jaw mechanisms are integral to how the Wen Lathe Drill Chuck grips drill bits. They come in various designs, with the most common types being three-jaw and four-jaw chucks. The three-jaw chuck is popular for its ability to center round, square, and hexagonal shanks, making it a versatile choice for different applications. This type's key characteristic is its symmetrical design. This symmetry offers balanced holding power, reducing vibration during operation.
In contrast, the four-jaw chuck excels in holding irregularly shaped objects. It allows for more precise adjustments since each jaw can be moved independently. This unique feature of individual jaw movement offers the advantage of securing workpieces of various shapes and sizes effectively. However, the complexity of the four-jaw mechanism may require more setup time.
Jaw Adjustability
Jaw adjustability significantly affects the performance of the Wen Lathe Drill Chuck. The adjustability feature allows the user to change the distance between the jaws, ensuring that they can accommodate different sizes of drill bits or workpieces. This flexibility is particularly beneficial when switching between various tasks or materials.
One prominent characteristic of the jaw adjustability is the ease of use. With many modern chucks, jaws are designed for quick adjustments without specialized tools, promoting efficiency in workflow. However, users must pay attention to the calibration to prevent misalignment, which can lead to inaccuracies in machining.
Chuck Key and Drive Mechanisms
The chuck key and drive mechanisms also form crucial parts of the Wen Lathe Drill Chuck system. The chuck key is used to lock and unlock the jaws quickly. A well-designed chuck key ensures that users can operate the chuck smoothly, enhancing both safety and convenience.
In terms of drive mechanisms, various types exist. Traditional keyed chucks rely on a universally designed key to open and close the jaws. In contrast, keyless chucks enable users to operate the chuck without needing an additional tool. This simplicity can be advantageous in instance where speed and ease are paramount. Understanding these drive mechanisms can enhance user experience and efficiency during machining processes.
Types of Wen Lathe Drill Chucks
Understanding the different types of Wen lathe drill chucks is crucial for selecting the right tool for machining tasks. Each type offers unique features and benefits that can affect precision and ease of use. This section will cover three main types: Keyed vs. Keyless, Multi-Jaw Chucks, and Specialized Chucks.
Keyed vs.
Keyless
Keyed chucks utilize a chuck key to tighten and loosen the jaw grip on the tool bit. This mechanism allows for a strong clamping force, making it suitable for high-torque applications. In contrast, keyless chucks offer a rapid adjustment system, allowing the user to quickly change bits with a simple twist of the chuck body.
Advantages of Keyed Chucks:
- Enhanced stability: Provides a firmer grip on the bit, reducing slippage during machining.
- Torque handling: Ideal for heavy-duty tasks where high torque is common.
- Precision: Ensures tight clamping, enhancing accuracy in drilling.
Advantages of Keyless Chucks:
- Speed: Faster bit changes, minimizing downtime.
- Convenience: Easier to operate, especially for frequent bit swaps.
- Versatility: Useful for various light to medium-duty applications.
Both options are valid, but the choice largely depends on the specific requirements of the task at hand.
Multi-Jaw Chucks
Multi-jaw chucks, typically featuring three or four jaws, provide superior grip and alignment. They are especially advantageous for holding irregularly shaped work pieces securely during machining. Unlike traditional two-jaw chucks, multi-jaw chucks distribute pressure uniformly around the tool, minimizing deformation.
Benefits of Multi-Jaw Chucks:
- Versatile clamping: Able to secure a variety of shapes and sizes.
- Increased stability: Provides a balanced grip on the workpiece, reducing vibrations.
- Precision work: Allows for more precise machining due to enhanced centering capabilities.
These chucks are particularly useful for complex machining tasks that require precision and stability.
Specialized Chucks
Specialized chucks cater to specific needs in machining. Two key types within this category are Collet Chucks and Drill Inserts.
Collet Chucks
Collet chucks are designed to hold cylindrical workpieces with a high degree of accuracy. They use a collet to grip the tool bit, which expands when tightened. The main advantage of collet chucks is their precision in holding tools, making them favorable for fine detail work.
Key Characteristic: The ability to hold tools with minimal runout.
Benefits:
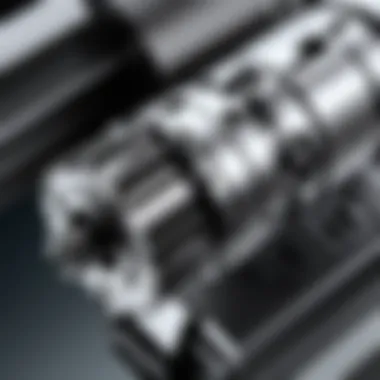
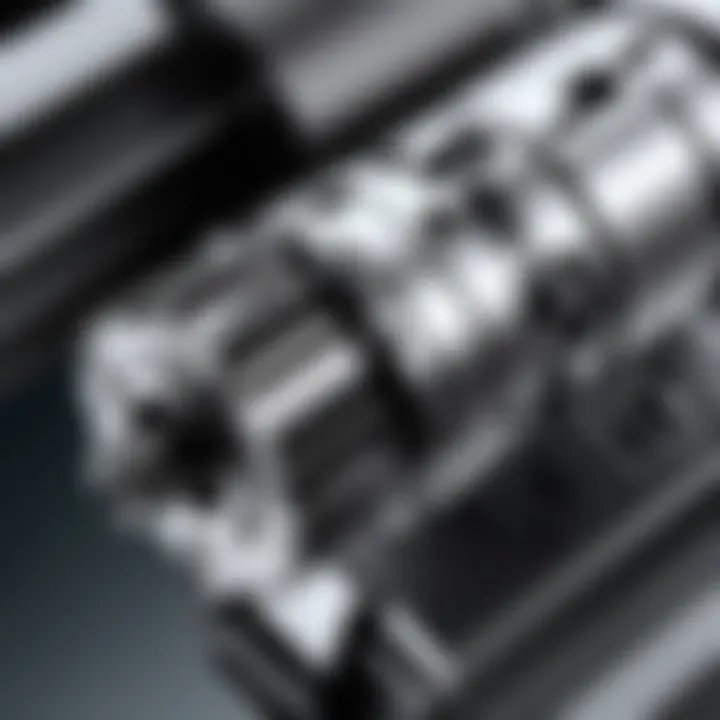
- Accuracy: Ideal for precision drilling and milling.
- Flexibility: Suitable for various shank sizes and types.
However, changing bits can take longer compared to keyless options, which might not be ideal for all applications.
Drill Inserts
Drill inserts, on the other hand, are specialized tools designed for specific drilling operations. They feature replaceable cutting edges, which can be adjusted for different operations. This makes drilling inserts adaptable and cost-effective.
Key Characteristic: Easy replacement of worn-out cutting edges.
Advantages:
- Cost efficiency: Only the insert needs replacement rather than the entire tool.
- Customizability: Options available for different materials and applications.
Drill inserts are particularly beneficial for users seeking a long-lasting and efficient solution for varied drilling tasks.
Installation of Wen Lathe Drill Chucks
Proper installation of a Wen lathe drill chuck is crucial for optimal performance and safety during machining operations. The importance lies not only in ensuring that the chuck functions efficiently, but also in preventing accidents that could arise from improper setup. A correctly installed chuck enhances precision and makes the lathe easier to operate. It is essential to understand the steps involved in the installation process, as well as common pitfalls to avoid.
Preparation Steps
Before beginning the installation of a Wen lathe drill chuck, certain preparatory actions should be undertaken.
- Gather Necessary Tools: It is important to have all the required tools on hand. This typically includes the chuck key, a wrench, and possibly a lubricant or cleaning cloth. Having everything ready before starting can make the process smoother.
- Select the Right Chuck: Ensure that you have the correct drill chuck for your specific lathe model. The chuck must fit snugly on the lathe's spindle to function properly.
- Clean the Spindle: A clean spindle helps achieve a better grip and fit. The area should be free from debris and old lubricant. Use a cloth to wipe the spindle clean.
- Inspect the Chuck: Check the drill chuck for any damages or defects. Look for cracks or worn-out parts that might affect its performance. If anything seems amiss, it is better to replace the chuck before installation.
Mounting Techniques
Mounting the Wen lathe drill chuck requires careful attention to detail. Follow these steps for effective mounting:
- Align the Chuck: Position the drill chuck over the lathe spindle. Ensure that the chuck is aligned correctly with the spindle to avoid any imbalance during operation.
- Tighten the Chuck: Use the chuck key to tighten the chuck onto the spindle. Make sure to apply steady pressure but avoid overtightening, which can damage both the chuck and spindle.
- Check the Alignment: After tightening, rotate the chuck by hand to check for any wobble or misalignment. An imbalanced chuck can cause issues during machining.
- Secure the Lathe Setup: Once satisfied with the alignment and tightness, ensure the entire lathe assembly is secure before powering it on. This step is vital for safe operation.
Common Mistakes to Avoid
When installing a Wen lathe drill chuck, certain common mistakes can lead to inefficiencies or accidents. Here are a few to be aware of:
- Skipping Cleaning Steps: Failing to clean both the chuck and spindle can lead to poor gripping and potential slippage during operations.
- Neglecting Inspectons: Not checking for damage before installation could result in using a defective chuck, which poses risks.
- Overtightening: Applying excessive force can strip threads or crack the chuck, leading to costly repairs.
- Ignoring Alignment: Misalignment during mounting can create vibration and reduce precision, affecting the quality of work.
Ensuring a methodical approach to installation and avoiding these mistakes will lead to better outcomes in lathe operations.
Maintaining the Wen Lathe Drill Chuck
Proper maintenance of the Wen Lathe Drill Chuck is crucial for ensuring its reliability and longevity. By taking care of this tool, users can enhance precision in machining operations and reduce the chances of damage or malfunction. Regular attention to maintenance can also lead to improved performance and efficiency during various tasks. Given that these chucks are central to the operation of a lathe, neglecting their upkeep can result in costly errors or delays.
Regular Inspection and Cleaning
Regular inspection of the Wen Lathe Drill Chuck is pivotal. Users should routinely check for any signs of wear or damage. Look for cracks, excessive rust, or other abnormalities in the body and jaw mechanisms. A close examination can often catch problems before they escalate. Keeping the chuck free from debris is essential. Dirt and metal shavings can interfere with the jaws, leading to inaccurate drilling.
Cleaning can be performed using a soft cloth. For tougher residues, use a mild solvent. After cleaning, ensure that the chuck is thoroughly dried to prevent rust formation. A simple cycle of inspecting and cleaning enhances the chuck's reliability and extends its lifespan.
Lubrication Practices
Lubrication is another fundamental aspect of maintaining the Wen Lathe Drill Chuck. Proper lubrication reduces friction between moving parts, ensuring smoother operation. For most chuck types, a light machine oil should be adequate. Apply a few drops to the jaw mechanisms and other moving components. This will help keep them from seizing over time.
Timing is important here. Lubrication should be done after cleaning and inspection. Doing so ensures that the elements are free of contaminants that could lead to wear. Additionally, the frequency of lubrication depends on usage. If the chuck is used heavily, consider lubricating it more often to maintain optimal performance.
Troubleshooting Common Issues
Though the Wen Lathe Drill Chuck is a reliable tool, problems can arise. Some common issues include the chuck not gripping the drill bit properly or difficulty in opening and closing the jaws. If gripping problems occur, inspect the jaws for any damage or dirt trapped between them. Often, a thorough cleaning resolves this issue.
If the jaws are stuck, applying penetrating oil may assist in freeing them. Always allow time for the oil to work before attempting to move the jaws again. In instances where the chuck has become dislodged from the lathe, ensure it is properly remounted according to the user manual.
Regular maintenance not only prolongs the lifespan of the chucks but allows for continued precision in machining tasks.
In summary, maintaining the Wen Lathe Drill Chuck involves regular inspection and cleaning, proper lubrication practices, and addressing common issues proactively. By adhering to these guidelines, users can ensure their drill chucks deliver optimal performance and precision in their machining endeavors.
Applications of Wen Lathe Drill Chucks
Understanding the applications of Wen Lathe drill chucks is crucial to grasp their significance in various settings. These chucks are not just components of a lathe; they are essential tools that enhance precision and efficiency in both professional and personal projects. This section will examine various applications of these chucks, highlighting their benefits and considerations.
Machining Operations
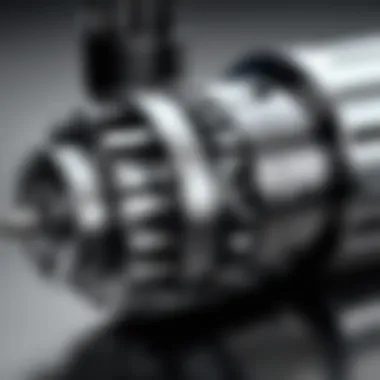
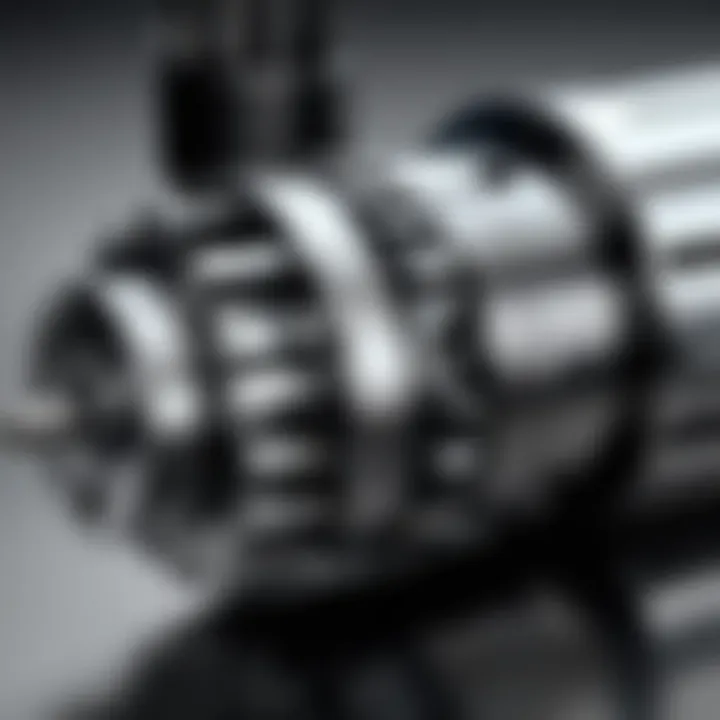
Wen Lathe drill chucks excel in machining operations. They secure drill bits with accuracy, which is vital for producing items with precise dimensions. The versatility of Wen drill chucks allows them to be used with a variety of tools, including twist drills, reamers, and taps. Using a drill chuck improves part repeatability and reduces the risk of errors. Precision in machining is indispensable, especially when creating parts for machinery.
Furthermore, the adaptable design of Wen drill chucks enables them to accommodate different sizes of drill bits. This feature is particularly useful in industrial settings where varying sizes may be required for different tasks. The ease of installation and removal means engineers can switch bits swiftly without losing time.
DIY Projects and Hobbies
For hobbyists and those engaged in DIY projects, Wen Lathe drill chucks offer significant advantages. They empower users to experiment and create with greater ease. Whether it's crafting wooden furniture or assembling models, the proper chuck can make a difference in the overall quality of the work.
Using a Wen drill chuck allows amateur builders to handle a variety of materials, making their projects more expansive. The ability to securely hold drill bits means fewer mistakes, which translates to better outcomes. These chucks also provide the reliability that hobbyists seek, allowing for a smoother and more enjoyable crafting experience.
Industrial Use Cases
In industrial applications, the Wen Lathe drill chuck proves to be an indispensable tool. Manufacturing facilities often rely on these to maintain efficiency in their operations. With precision comes the capability of producing mass quantities of parts without compromising on quality. Industrial use cases include automotive part production, aerospace components, and electronics manufacturing.
Another important aspect is the adaptability of the Wen drill chuck to different machining environments. Its compatibility with various machines enhances operational flexibility and reduces setup times. By providing consistent performance across various applications, these drill chucks can significantly impact productivity.
Key Insight: The integration of Wen Lathe drill chucks in both amateur and professional setups speaks to their versatility and importance in achieving precision and efficiency.
Comparative Analysis with Other Drill Chucks
In any discussion surrounding drill chucks, it is essential to perform a comparative analysis to overview their respective strengths and weaknesses. This section does not only highlight the nuances between different chucks but also underscores the value each type brings to the machining process. A thorough analysis benefits end users in selecting the most suitable drill chuck for their specific applications, which in turn maximizes efficiency and precision.
Advantages of Wen Lathe Drill Chuck
The Wen Lathe Drill Chuck offers several advantages that make it a preferred choice among machinists. One notable feature is its reliable gripping power, which ensures that the tools remain securely fastened during operation. This warranty against slippage not only enhances safety but also improves accuracy in drilling tasks.
- Versatility: The Wen Drill Chuck is compatible with various drill sizes, making it an adaptable choice for multiple tasks. This flexibility assists users in switching between different projects without needing various chucks.
- Ease of Use: Its design often allows for easy installation and adjustment. This user-friendly aspect makes it accessible even for those who might not be seasoned professionals.
- Robust Build Quality: The construction materials used in Wen chucks are often durable, resisting wear and tear over time. This longevity is a critical factor for consistent performance in demanding applications.
Limitations and Considerations
While the Wen Lathe Drill Chuck is advantageous, users should also recognize its limitations. Understanding these aspects can help in making informed decisions, and using the chuck effectively.
- Weight: Some users find that Wen chucks can be slightly heavier compared to others, which may affect the balance if used in lightweight setups.
- Compatibility Issues: Although generally versatile, certain models may have fitment issues with specific lathe systems or drill bits. It’s essential to confirm compatibility before purchasing.
- Price Point: The cost of Wen chucks might be higher than some generic options. For users on a budget, this could be a decisive factor. However, it’s essential to weigh the long-term savings of durability against initial expenses.
In summary, understanding the advantages and limitations of the Wen Lathe Drill Chuck provides a clear perspective on its capabilities.
By analyzing various drill chucks, one can make a more educated decision that aligns with project requirements and personal preferences. This kind of thoughtful selection enhances the overall experience in machining operations.
Future Trends in Drill Chuck Technology
The realm of drill chuck technology is evolving rapidly, fueled by advances in materials and electronics. These trends are reshaping the way users approach their machining tasks with aim to enhance precision and ease of use. Understanding these changes is essential for anyone invested in lathe operations.
Innovations in Design
Recent innovations in the design of drill chucks have focused on efficiency and user-friendly features. One key trend is the use of lightweight yet strong materials such as carbon fiber and advanced composites. These materials help reduce overall weight without compromising strength. This is particularly vital in high-speed applications where every gram counts.
Some innovative aspects include:
- Ergonomic Features: New designs incorporate hand-friendly shapes, making it easier for users to apply necessary torque.
- Self-Centering Jaws: They ensure that the drilled materials are held with optimal grip and precision, reducing the risk of vibrational issues.
- Quick Release Mechanisms: Allow for faster bit changes, significantly increasing workflow efficiency.
Such advancements not only enhance functionality but also minimize wear and extend the lifespan of the chuck. This drives down maintenance costs and improves overall user satisfaction.
Integration with Smart Tools
Integration of drill chucks with smart tools is another trend gaining traction. As technology becomes more interlinked, the importance of connectivity in manufacturing processes cannot be understated. Smart drill chucks equipped with sensors can now provide real-time data on performance and wear.
- Data Analytics: These smart chucks collect data that operators can analyze to optimize their machining processes. Such data can involve torque measurements, operational hours, and even feedback on the material being worked on.
- Remote Monitoring: By connecting to mobile devices or computers, users can have instant access to the operational state of their equipment, leading to proactive maintenance strategies.
Additionally, the integration encourages the development of predictive maintenance policies. This ensures prolonged usability and less downtime, a critical factor in industrial environments.
The integration of innovations will lead to better efficiency, versatility, and ultimately will impact productivity positively.
Ending
The conclusion of this article plays a vital role in summarizing the intricate details surrounding the Wen Lathe Drill Chuck. It serves not only as a recap but also as a final synthesis of the key points discussed throughout the piece. Understanding the significance of the Wen Lathe Drill Chuck in both professional and DIY contexts cannot be overstated. The chuck is not merely a component; it is central in ensuring precision and efficiency in machining tasks.
Summary of Key Insights
Throughout this guide, several key insights emerge regarding the Wen Lathe Drill Chuck. First, its construction and various mechanisms provide adaptability across different machining operations, which is indispensable for achieving best results. The guideline on installation and maintenance highlights how regular care can prolong a chuck's lifespan and sustain optimal performance. Furthermore, understanding the differences between chuck types informs users in their selection process, guiding them toward the best fit for their needs. Each aspect contributes to enhancing overall machining efficacy.
Final Thoughts on Selection and Usage
In closing, potential users should approach the selection and usage of Wen Lathe Drill Chucks thoughtfully. Consider factors such as material compatibility, size, and the specific requirements of the project at hand. Practical usage knowledge can transform a basic understanding into effective application. Therefore, continual learning and adapting to new advancements in chuck technology can offer significant improvements in precision machining.
A well-chosen and maintained drill chuck not only elevates the quality of work but also increases productivity and ensures safety.
By integrating these elements—knowledge of components, application scenarios, and maintenance practices—users can make informed decisions and foster improved outcomes in their machining tasks.